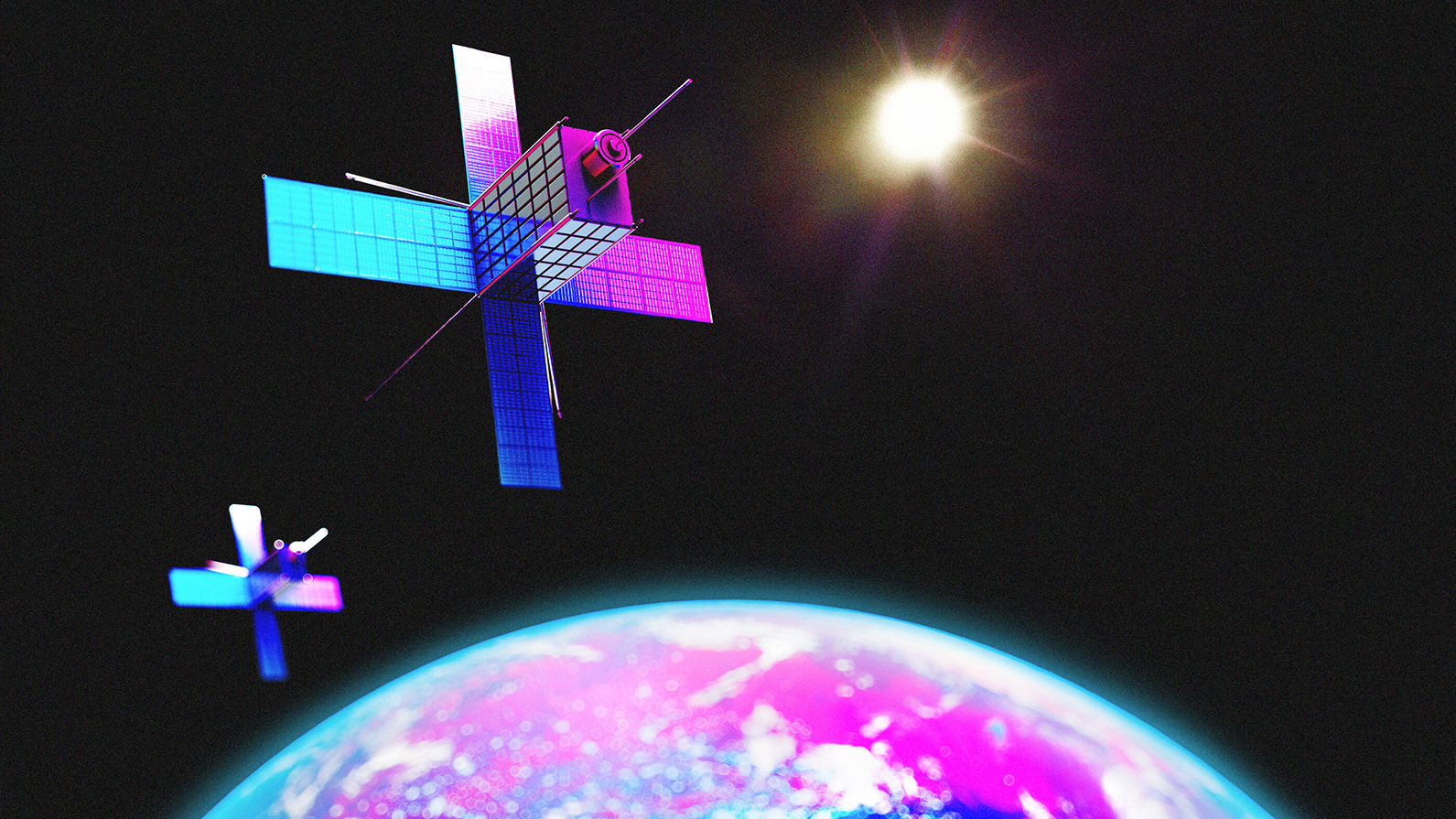
Below is an overview of Space Forge’s approach to future Carbon Dioxide reduction in Earth’s atmosphere and responses to our FAQs.
As a company, we intend to exploit the unique environment found in low orbit around the Earth to create new and improved supermaterials that can directly benefit life on the ground.
The abundant ultra-vacuum and microgravity conditions found in Space can be used to create superior quality crystals and alloys that, when returned to Earth, will enable terrestrial high-energy consuming industries to decarbonise faster and more cost effectively.
Space Forge is building the ForgeStar® family of uncrewed manufacturing satellites to enable the green industrial revolution using Space.
How will the products save energy?
Space Forge is focused on improving the energy efficiency of current terrestrial systems by creating small amounts of ultra-pure materials with near-perfect internal structures for use inside the critical heat generating components. Examples of this are given below:
High frequency amplifiers
Space Forge is specialising in the production of wide and ultra-wide bandgap semiconductors. This class of semiconductor offers superior performance1 over Silicon and are being adopted worldwide for high frequency amplifiers.
The amplifiers inside a typical cell tower use only a few milligrams of semiconductor material but over 55% of the power consumed in the tower is lost inside this material. Earth made semiconductor materials are prone to defects during manufacture caused by contamination from the atmosphere and gravity induced rotation in the crystal lattice. These defects prevent heat from flowing out of the semiconductor, causing it to heat up and become less efficient which in turn causes it to heat up more. This thermal runaway effect shortens the life of the semiconductor and requires significant cooling systems to prevent the amplifier from failing - which in turn consumes more energy.
The total energy consumption in a cell tower using Earth made materials can be in excess of 11W for every 1W of data transmitted. When applied to the estimated 5 million cell towers worldwide2 this accounts for approximately 39 MegaTonnes of CO2e (equivalent) emissions per year - equivalent to a mid-sized European country like Ireland & Switzerland3.
Replacing the milligrams of semiconductor material inside these amplifiers with space made versions which, due to production in the “ultimate cleanroom” of the space environment, have significantly fewer defects and hence better thermal conduction and overall efficiency. It is estimated, based upon previous in-orbit studies done on semiconductor growth, that space made amplifiers can more than halve the total cell tower consumption to around 5W for every 1W of data transmitted. A single flight of Space Forge’s ForgeStar vehicle configured to manufacture this type of semiconductor material can produce enough to outfit over 90,000 next generation cell towers which over an assumed ten year lifetime could save an estimated 4.3 MegaTonnes of CO2e from ever having to be emitted.
Super alloys for aircraft turbines
The efficiency of jet aircraft engines is determined in large part by the length of the turbine blades, which in turn is limited by the strength of the material. In the case of jet engines the state of the art turbine blades are made from nickel based superalloys or ceramics which can retain strength under extremely high temperatures.
These materials rely on low contamination, particularly from atmospheric oxygen, to ensure they are not brittle and also on Earth suffer from gravity driven buoyancy effects when mixing materials of different density together. In space the oxygen levels are near zero and the microgravity environment eliminates buoyancy, allowing superior single crystal alloys and ceramics to be made. The manufacture of ceramic turbine blade material inside the International Space Station has already been demonstrated. Space Forge’s ForgeStars offer a further improvement over the ISS by flying in a higher orbit; moving to a true oxygen free environment.
Space made turbine blades could be 30-50% lighter4 than current state of the art materials which could lead to an overall 10% increase in jet aircraft efficiency. For a typical 747-400 jet this increased efficiency would translate to a lifetime5 saving of ≈200,000Tn6 of aviation fuel which is ≈630 KiloTonnes of CO2e emissions saved per aircraft.
Doesn’t travelling to space and back emit a lot of CO2?
The designing, building, testing and launching of satellites is a high energy intensity activity, but no studies of the emissions of the complete space industry are currently available. Since its formation Space Forge has been attempting to measure its CO2e emissions through supply chain evaluation, comparisons to other industries and employee surveys. Space Forge also commissioned a study with the Federal Institute of Rio Grande do Sul (IFRS) to estimate the CO2 emissions of common launch vehicles.
As of Jan 2024 Space Forge estimates that its activities to date have emitted a CO2e of 200 Tonnes, accounting for staff commuting, business travel, launches, office energy and subtracting direct offsets such as carpooling, use of electric cars and renewable energy available to home working staff. There is an estimated net production of 331kg of CO2e per day. This does not yet include the emissions of our supply chain but Space Forge has the ambition to do this in the near future.
It can be seen that the two largest sources of emissions currently are employee commuting and launches, therefore Space Forge is focused on reducing both by having a paid employee carpooling scheme and prioritising more efficient launch vehicles based upon the IFRS study.
It is estimated that when flying each ForgeStar mission will consume approximately 283 Tonnes of CO2e, when including the emissions of the satellite build, launcher build, launcher fuel and transport logistics. Once in orbit the satellite exclusively uses solar power to generate materials and any waste products are responsibly disposed of. At the end of each flight 100% of the satellite is brought back to Earth for refurbishment and re-use.
As described above, it is possible for a single ForgeStar flight to produce products that would prevent up to 4.3 MegaTonnes of CO2e from ever having been emitted; and so when compared to a 283 Tonnes consumption this is an overall emissions reduction ratio of approximately 1:15,000.
What about space debris?
Unlike all other re-entry vehicles flying today, ForgeStars are designed to return 100% of their mass (minus consumed fuel) to Earth at the end of a flight, which leaves no space debris in orbit. During re-entry the ForgeStar uses an innovative deployable non-ablative heat shield which does not release any waste products into the atmosphere. After landing the ForgeStar will be recovered by a Space Forge team and refurbished ready for the next flight. If a ForgeStar was to fail in-orbit to a level where it cannot be safely recovered, it will burn up in Earth’s atmosphere within timelines set by international standards on the reduction of space debris.
Isn’t this greenwashing?
Space Forge is a team who care about their impact on the environment. If it were possible to produce these next generation materials on Earth without the need to travel into Space we would, but 20 years of research on the ISS has shown an undeniable fact; crystals grow better in microgravity.
In order to prevent catastrophic climate change three approaches are urgently needed; 1) reducing the amount of energy society consumes, 2) switching from fossil fuels to renewable energy and 3) capturing CO2 from the atmosphere. Space Forge is focused on the first approach which is the most impactful in the short and long term. Pristine and uncontaminated crystal materials like semiconductors and alloys are integral to reducing CO2 through both reduced energy consumption and increased reliability which leads to less waste. They can also support the high power switching needs of future green energy microgrids - accelerating the transition from fossil fuels.
Despite the energy saving potential of our products, this does not give Space Forge a free pass to ignore its own CO2 emissions and so we are committed to reducing our internal carbon footprint by focusing on employee commuting, launch emissions and the reusability of our satellites.
Is this just a niche solution?
Space Forge firmly believes that Space will soon be recognised as the ideal environment for the manufacture of next generation super materials, an activity that will in the second half of this century be a vital part of the Earth economy. Semiconductors, fibre optics, alloys, pharmaceuticals, vaccines are all based around crystal structures and are sensitive to contamination in their production; making Space the ideal place to make them. The price of launch is on a steep decline7 with the introduction of reusable rockets and the building of solar array farms in space is on the horizon8. When combined the number of products that can be economically made in space increases exponentially and so do the potential environmental benefits for Earth. In the long term Space Forge would like to see all polluting industries moved into orbit, making use of asteroids rather than Earth mined materials, to realise the ultimate goal of making Space work for humanity.
1 https://www.powerelectronicsnews.com/will-darwinian-evolution-allow-ultra-wide-bandgap-uwbg-semiconductors-to-displace-current-wide-bandgap-wbg-materials/
2 https://www.scientificamerican.com/article/cellular-towers-moving-to-solar-power/
3 https://www.worldometers.info/co2-emissions/co2-emissions-by-country/
4 https://redwirespace.com/newsroom/ceramics-manufacturing/
5 Assuming 35,000 cycles of 5556km
6 https://www.carbonindependent.org/22.html
7 https://futuretimeline.net/data-trends/6.htm
8 https://www.esa.int/Enabling_Support/Space_Engineering_Technology/SOLARIS/Space-Based_Solar_Power_overview